PDM和ERP是在企业信息化过程中发挥重要作用的系统,随着它们的发展,两者出现了功能上的交叉,当同时维护相同部分数据时就可能出现数据不一致的情况,而且信息无法在两个系统之间相互交流,这些障碍严重制约了信息化的发展。PDM中的产品数据是ERP系统的数据源头,产品数据的不准确,将直接影响ERP实施效果。因此需要实现PDM和ERP集成,打通两大系统之间的壁垒,消除信息孤岛,构建设计生产一体化的管理平台。那么PDM与ERP集成较难的是什么? 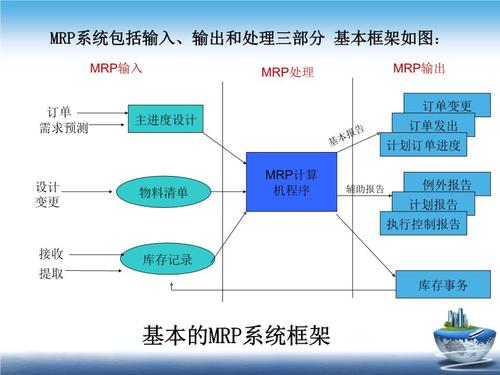 1、关于编码 首先来说说编码问题。2003 年笔者刚刚入行的时候,到一个企业实施 CAD 系统,这个企业正好启动实施ERP系统,实施ERP系统碰到的首要问题就是编码。企业为此专门花了20万的咨询费,请一个咨询公司做了一套编码体系,然后内部成立了一个6人的编码小组,专门负责编码的实施和推进工作。当时因为要将所有的零部件代号都按照新的编码规则统一重新编码,因此笔者和编码小组的组长有了许多交流的机会。这个企业的物料编码十分复杂,总共有24位,划分成了5段,每段都有不同的含义。但基本规则就是“大类 小类 流水”。编码刚刚在开发部门一实施,技术人员就炸了窝,他们异口同声地反对新的编码,理由只有一条一一看不懂。 以前零部件的编码是隶属码,看到零部件的代号就知道这个零部件是哪个产品上的,换成了新的编码以后,只知道这个零部件大概是盘类铸铁件,属于哪个产品则无法分辨。不仅开发人员不知道,车间生产人员也不知道,所以经常给技术人员打电话,询问手上的图样到底是哪个产品上的。 在吵架一般的讨论会上,编码小组的组长说了一句让我至今记忆犹新的话:编码是给电脑看的,不是给人看的!后来他跟我说,实际 ERP 上线以后,ERP 会根据编码告诉你这个零件是属于哪个产品上的,无需人工判断。 2009 年,德国的肖塔纳教授来华讲学,他的观点更直接:抛弃这种带分类关系的含义码,直接用流水码!肖塔纳给出的直接证据就是,德国很多企业,用了十几年ERP系统,后来用不下去了,原因就是随着业务的逐渐扩大,发现原有的含义码无法支撑下去,简而言之就是“编码爆炸”! 以前在手工管理的时代,编码有两个作用:一个是定义物料的惟一性,另外一个就是查询。但是到了信息化时代,查询手段丰富了,只要维护得当,用户可以很容易地通过材料、外形尺寸和加工方式等属性找到自己想找的物料。现在PLM 系统有类似 Google 的查询方式,任意输入一个信息,就可以将他有权限看到的图样和技术资料等信息查询出来。 因此,实施了PDM或者ERP系统之后,编码的查询作用降低了,只剩下一个标识惟一性的作用,用流水码就可以完全满足业务管理的需要。 不管企业如何编码,在 PDM 与 ERP 集成时,需要考虑如何统一 PDM 和ERP 中的零部件编码。如果企业先上的ERP系统,那么编码有可能由ERP系统来分配,需要在PDM中建立与ERP系统相同的零部件编码体系,使PDM和ERP中的零部件编码保持一致。但如果企业先上了PDM,由于CAD/PDM是设计数据的源头,那么设计数据的编码由PDM系统自动分配是非常合理的。 2、关于BOM 解决了编码的问题,再来解决BOM的问题。BOM一直是一个争议不断的话题,原因在于,每一个系统,每一种业务,都有专属的根据自己要求定义的BOM。ERP 系统中的MBOM,表达的是要把这个产品生产出来需要哪些物料。 但是实际上这个BOM仅仅是从生产的角度出发,满足了生产部门的要求,而采购部门需要看到的是完成这个产品到底需要采购些什么原材料(主材),这就形成了一个采购BOM;营销部门希望看到哪些零部件是可以单独销售的,这就形成了一个销售BOM…因此笔者“胆大包天”地重新定义一下BOM的概念:BOM就是根据各业务部门的需要形成的产品信息的视图。 通过对BOM概念的重新定义,我们不难发现,实际上过去那种一味要求某—个BOM向另外一个BOM转换的做法,是值得商榷的。实际上BOM不过是各种产品零部件信息的“再组合”,只是组合的条件不同而已,不过不论这些信息怎么组合,这些信息都有一个基本来源,那就是设计开发。因此在PDM里管理和根据要求组合这些BOM是合适也是安全的做法。简单来说,就是设计开发人员在PDM中维护好设计BOM信息,其他部门的人则根据需要到PDM里面组合自己希望得到的BOM信息,然后再导入到自己的系统当中。需要说明的是,这种组合可以是自动进行的(在规则明确的情况下),也可以是手动的,但并不一定越自动越好。 在日朝PDM系统中,产品结构树从产品设计的角度来表达产品零部件的组成关系,工艺人员可以在此基础上添加工艺信息,将一个面向设计的产品结构树转化为面向制造的结构树。通过产品结构树的不同形态(视图),可以得到企业不同职能部门需要的设计 BOM、装配 BOM、采购 BOM 等。 通过引入“设计虚件”的概念,通过产品配置,可以快速地从原型产品演化出系列化的变型产品,大大提高开发效率和质量。 3、关于工艺 需要解决的问题是工艺信息的问题。众所周知,工艺是连接设计和制造之间的桥梁和纽带,ERP里进行MRP运算所需要的大部分信息都来自于工艺,因此在 PDM与ERP集成上,工艺是无法或缺的一环。但是在实际操作时,工艺信息往往没有得到足够的重视。 不够重视主要体现在两方面:首先是工艺信息不全。举例来说,在实施ERP 时,往往需要定义“工作中心”,但是在传统工艺中,是没有工作中心这个概念的。这样以来,ERP需要工作中心的数据,但是工艺部门又不知道如何提供,这种信息的不对称让很多ERP都无法深入应用:其次是信息不准确。 比如,过去指定某个零件的某个工序需要到某种型号的机床上加工,并对加工的工时进行了规定,但是真正执行的时候,未必完全按照工艺的要求执行。其中原因一方面是车间对工艺纪律管理不够到位,另外一方面也凸显出工艺信息的不够准确,无法指导车间的实际生产。 一旦实施了ERP以后,这个问题可能就比较严重,因为如果进行工序级的排产,那么设备和工时都是非常关键的排产信息,如果这些信息不准确,那么工序的排产计划无疑是无法执行的。 因此要破解PDM与ERP之间的集成难题就必须重视和规范工艺信息,而将工艺信息结构化是重中之重。结构化的信息才能与ERP等其他系统进行对接,才能够较为容易地保证信息的一致性。 日朝PDM的工艺管理模块,可以搭建结构化零部件工艺BOM,包括机床设备、工艺装备、工作中心、工时定额切削用量以及工艺文档等工艺信息。通过与 ERP 集成可以将这些工艺信息传递到 ERP 系统中。 4、日朝PDM与ERP集成方案 日朝PDM提供与金碟、用友、鼎捷、速达、正航、SAP、QAD、傲鹏等主流ERP系统集成功能,实现物料库同步。PDM向ERP系统传递物料信息(包括编码信息)、BOM、工艺信息等生产所需的基础数据。设计过程中,PDM从ERP 系统中快速查询生产信息,如库存、原材料价格、半成品制造成本等,提供设计成本核算或报价使用,或消除库存积压。 1)日朝PDM向ERP系统传递物料信息、BOM、工艺信息等生产所需的基础数据。 2)设计过程中快速查询生产信息,PDM 从ERP 获取原材料价格、库存等信息。 无论是编码、BOM还是工艺信息,为了实现集成的目标,都有一个共同的方向,那就是一致性:设计信息、工艺信息和制造信息的高度一致,这是破解PDM 与ERP集成的前提。 日朝PDM系统通过ERP集成接口,实现产品数据的一致性,达到数据共享,把ERP系统所需要的、设计可提供的设计结果数据,很容易的从PDM系统传递到ERP系统,避免了由于数据重复输入造成的错误,并确保变更后数据的同步。通过集成打通两个信息孤岛信息传递,实现设计生产一体化。
信息发布:广州名易软件有限公司 http://www.myidp.net
|